在煤礦生產過程中,頂板事故占有較大比率,尤其是煤層頂板堅硬、完整、不易冒落綜采工作面初采,由于一般采取自然垮落法,隨著工作面的推進,造成采空區懸頂面積不斷擴大,當采空區大面積瞬間垮落時極易形成颶風和沖擊壓,造成人員傷亡和設備損壞。而且容易造成瓦斯瞬間涌出,誘發瓦斯重特大事故。因此,如何縮短綜采工作面初次來壓的步距,減少采空區懸頂面積,盡快充填采空區,是解決綜采工作面初次垮落的焦點問題。
1 地質條件
鐵法煤田煤系地層為中生界晚侏羅系地層,屬陸相沉積。巖相為湖泊相及河床相沉積,煤層頂板巖相和巖性變化較大。偽頂一般發育不完全,多為泥巖;直接頂發育較好,多為粗砂巖、中砂巖、粉砂巖、細砂巖。部分煤層及頂板有沖刷現象,局部為輝綠巖;煤層老頂類多為粗砂巖、中砂巖,堅硬、致密。煤田內地質構造以斷層為主,褶皺次之。煤系地層傾角平緩,一般在5°左右。首次采用深孔預裂爆破強制放頂技術的礦井為大隆煤礦,屬于多煤層群開采,煤層埋深350~600m,瓦斯等級為高瓦斯礦井。采用深孔預裂爆破強制放頂技術的工作面為E3402,該工作面位于東三采區的南側,為東三采區的首采面。工作面長167m,走向長508m。切眼與東二采空區毗鄰,最小距離10m,最大距離32m。工作面沿走向方向布置,沿傾向方向坡度小于5°,賦存條件相對簡單。切眼附近煤層厚度2.85m,無偽頂;直接頂板巖性為粗砂、中砂和細砂巖,巖性變化大,部分受河床沖刷,平均厚度5m,硬度系數f=5;老頂巖性為含礫粗砂巖,膠結松散,平均厚度24m。由于工作面以高硬度巖性為主,且膠結程度較高,初次來壓步距較長,因此,如不采取人工強制放頂的辦法,很難實現隨工作面推進而垮落。而大面積懸頂形成大的采空區空間,產生大量瓦斯積存,同時也增加了自然發火的因素,給安全生產帶來重大隱患。
2 放頂基本原則及方案設計
2.1 放頂基本原則
以破壞頂板的完整性為前提,根據直接頂、老頂的厚度及巖性特點設計放頂方案。在工作面兩順和切眼施工鉆孔,采用深孔預裂爆破技術,對初次來壓期間的頂板實施有效控制,盡可能使冒落的矸石充滿或基本充滿采空區,對上履巖層起支撐或墊層作用,達到使其隨采隨落的目的;同時破壞頂板的完整性,使上履巖層較易垮落,從而減弱了頂板垮落的沖擊強度,大大減少老塘有害氣體積存空間,從而降低因頂板垮落而造成瓦斯的瞬間涌出及頂板大面積垮落而形成沖擊壓力的可能性。
2.2 E3402工作面放頂方案設計
E3402工作面兩順、切眼為錨桿和錨索聯合支護,在安裝支架的同時,將切眼內錨桿、錨索的托盤全部卸下,以去除錨桿、錨索對頂板的支護作用。
(1)切眼內炮眼布置。工作面推進2.4m后,在支架后側采取臨時支護的情況下,施工兩排炮眼,呈三角形垂直頂板布置。孔深為2m,在支架前20~84號支架范圍內距煤壁1m打炮眼,與工作面垂直并向老塘傾斜仰角75°,間距3m,孔深6m,孔徑65mm,裝藥系數為0.6。
(2)兩順內炮眼布置。各布置兩組炮眼,呈上下兩層分布。兩組炮眼分別距切眼為15m和20m,每組3個孔,孔徑75mm,每孔裝藥量分別按孔,第一組孔深分別為12m、26m、26m,仰角分別為33°、17°、17°,與切眼水平夾角分別為27°、75°、90°。第二組孔深均為40m,仰角均為11°,與切眼水平夾角分別為75°、83°、90°,終孔距頂板6m。
3 施工方法
工作面切眼內炮眼采用3kW巖石電鉆施工,兩順炮眼采用ASZ-3A型抽放鉆機施工。采用高威力震源水膠藥柱,規格為Φ60mm×345mm。采用礦用瞬發雷管,礦用導爆索,聯線方式為串聯,配備QL-2000型強力起爆器起爆。在未起爆前留1m孔深作捆綁雷管與導爆索用。采用封土和封泥充填,炮眼充填系數為0.4。切眼內炮眼每次起爆5個孔,兩順每組6個孔同時起爆。兩順炮眼施工、裝配藥、裝配封土等工作需提前準備,炮眼施工完畢逐孔檢驗,編號記錄深度和藥包、封土、炮泥長度。工作面推進4.2~4.8m后開始裝藥,每孔裝藥和封土用導爆索或裝填木棍等參照物作好記錄,以保證各藥柱之間彼此密接,并對藥柱和封土作防滑處理。裝藥、封土至距孔口3m時,開始封泥2m,然后聯接雷管與導爆索,連線后一次起爆。
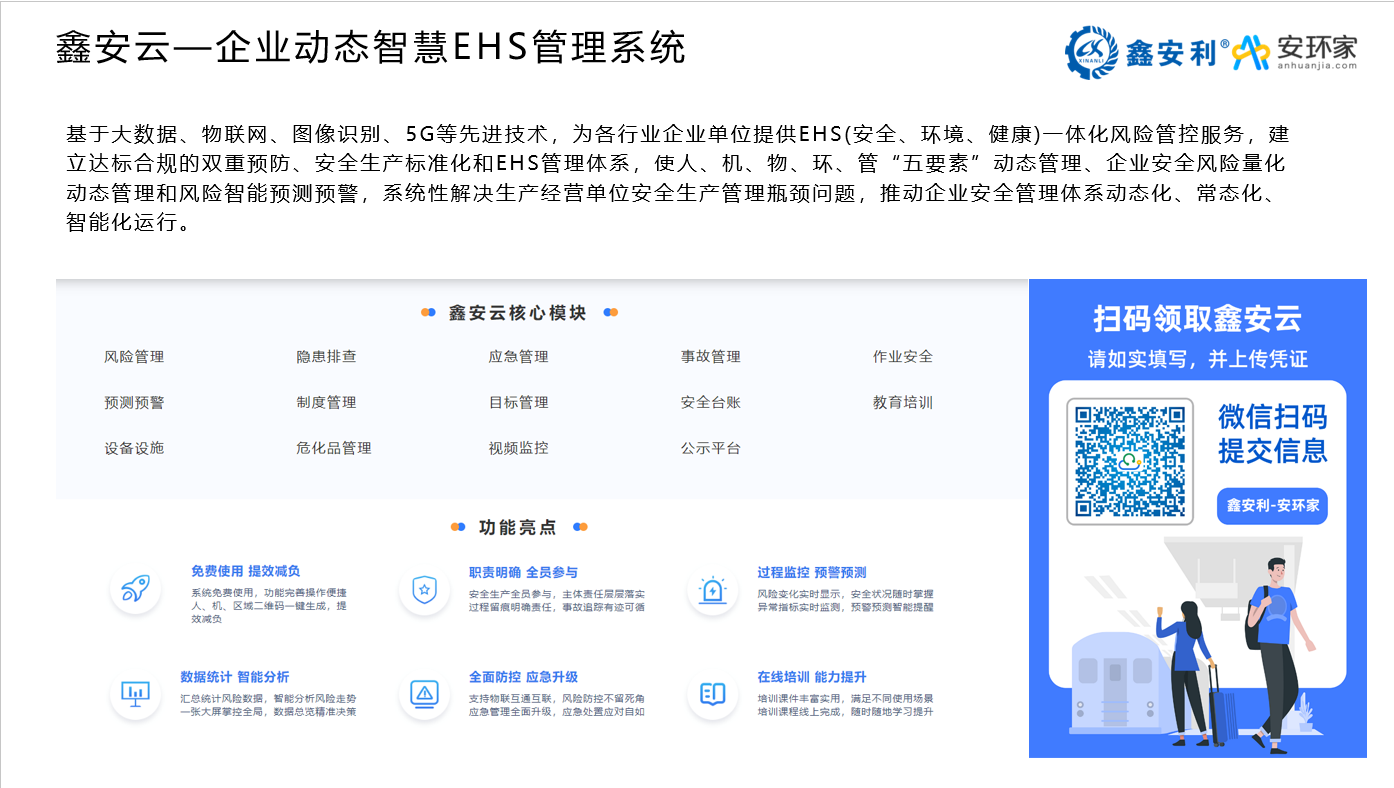